Maximizing Thermal
and Energy
Recovery
Maximizing Thermal
and Energy
Recovery
OVERVIEW
OVERVIEW
Lackeby Sludge Heat Exchanger
The Sludge Heat Exchanger (HSW) is a “Tube in Shell” sludge/water heat exchanger used to heat and cool biological sludge. The sludge tubes are a circular cross-section surrounded by rectangular cross-section water channels. The flow of the sludge and the water is cross-current for the highest efficiency. With the simplistic design, it makes maintenance straightforward and manageable.
The HSW utilizes a modular construction, with each heat exchanger being designed specifically for each application. There are five diameter sludge tube sizes available. There is the flexibility of one to four sludge tubes per level and 2 to 22 levels in the design. The sludge tubes can measure up to 20 feet in length. This design flexibility optimizes velocity, Reynolds number, shear rate, and pressure loss in the sludge flow for efficient heat transfer. This also provides flexibility in the physical size of the heat exchanger, as the design is easily modified to fit in an existing plant while still maintaining a relatively small footprint.
The units are constructed of high corrosion-resistant materials. The sludge tubes are 316 stainless steel. All of the other wetted material is Duplex stainless-steel alloy. The use of stainless steel provides a longer life and more efficient heat transfer than carbon steel. Additionally, the design of the sludge tubes ensures that large particles can pass and clogging risk is minimized.
The Sludge Heat Exchanger (HSW) has proprietary and innovative sludge turning chambers. These turn chambers have a small radius for a compact design. The mixing action in the turning chambers equalizes the thermal profile in the sludge tubes for more efficient heat transfer.

PRODUCTS
PRODUCTS
PRODUCTS
PRODUCTS
PRODUCTS
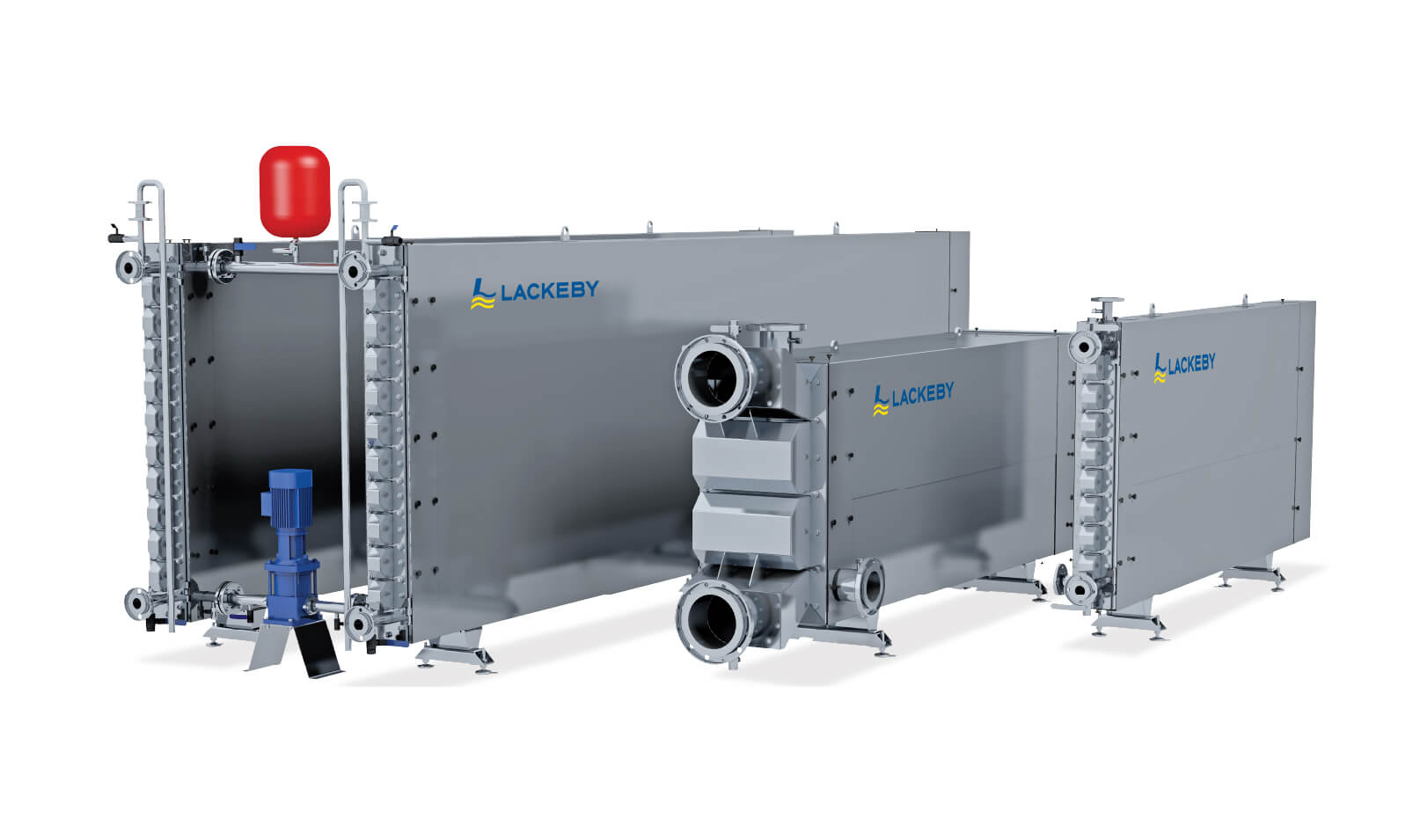


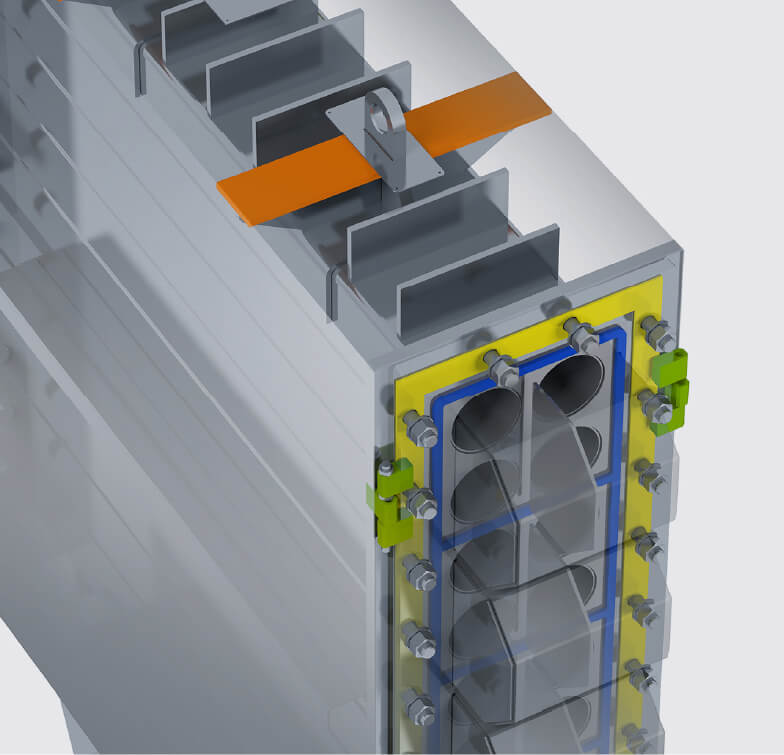

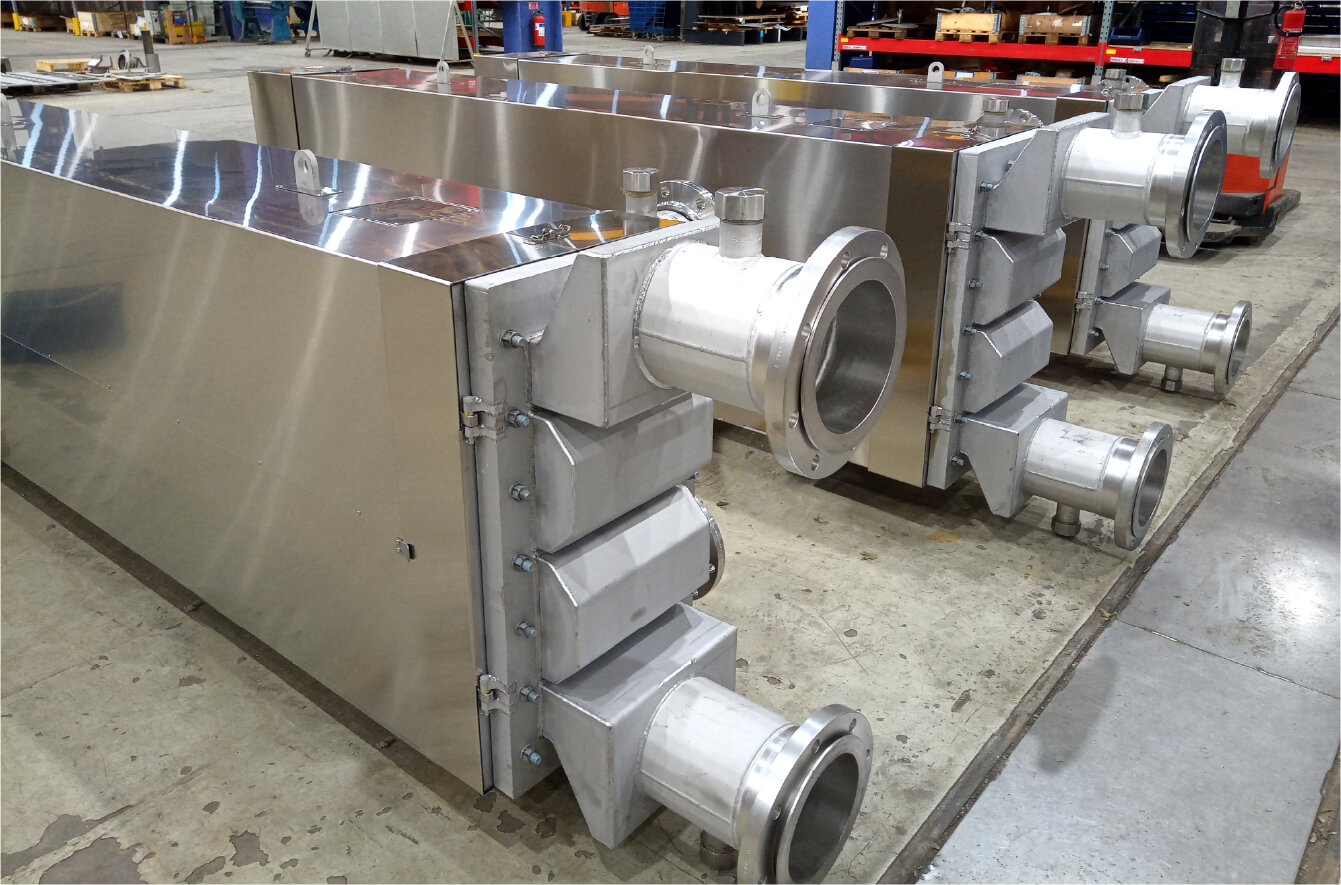

Features and Benefits
- The best ROI in the industry
- Modular design for high flexibility and configurability.
- High heat transfer with a small footprint and low pressure loss.
- Circular channels provide large throughput; low-pressure loss; and very low clogging risk.
- The compact design of the patented turn chambers not only provides a compact unit but also provides for more efficient heat transfer; easy installation; and simple maintenance.
- Hinged access doors on the end of each unit simplifies maintenance.
- All heat exchangers are constructed and tested in accordance with Section VIII, Division I, of the ASME Pressure Vessel Code.